Injection molding services near you
- Free DFM Feedback with Your Quote
- No minimum order quanties(MOQS)
- Products Tolerance can be ±0.005mm
- T1 samples AS Fast AS 2 Weeks
- Global delivery Door to Door
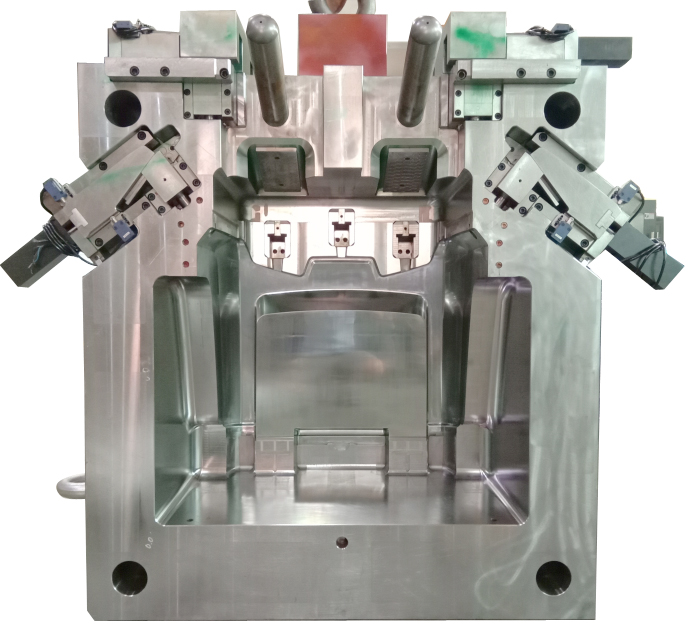
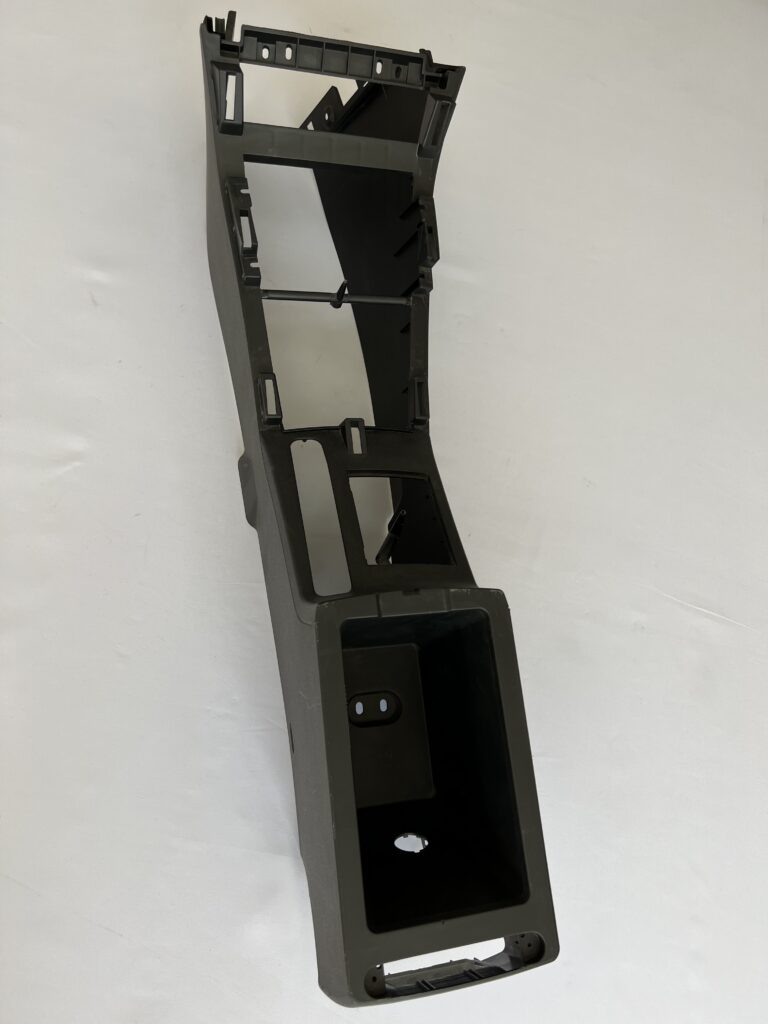
What are the advantages of injection molding service?
Injection molding is a plastic manufacturing process that allows for the mass production of high quality parts. It is typically used for small to high volume production, but our steel tooling can also make prototyping less expensive and get high quality plastic products.
- Low cost of obtaining high volume plastic parts,
- High quality plastic product quality with fully realized product structure and surface finish,
- Reproducible production,
- Complex plastic products can be manufactured,
- Reduced scrap rate at 1%,
- Large selection of thermoplastic and thermoset materials.
Who we are?
Muyoung mould was established in years of 2006, Muyoung starts business in exporting plastic mold and plastic injection molding product to worldwide customer.
We got ISO 9001-2008, IATF 16949 certification, and continuous investment in new equipment and management through innovation, Muyoung’ production capability can be 300 sets of molds and more than 10 million products per year.
Our diverse customer base includes, but is not limited to, major markets such as automotive, industrial/consumer, large appliances, forklifts, medical,electronics ,fuel delivery, packaging, Agriculture,furniture, construction and other……
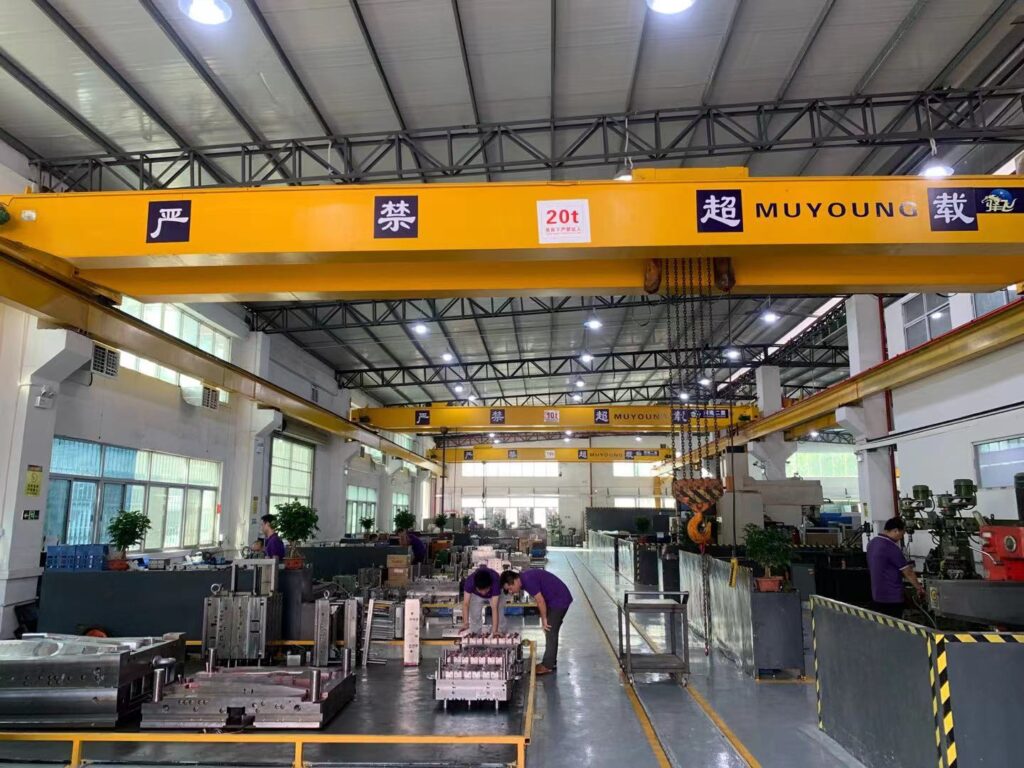
How we custom plastic injection molding for you?
At Muyoung, we value full partnership from the beginning of your manufacturing process to the end.
- Our project management provides feedback to clients to ensure parts are optimally designed for plastic manufacturing.
- We work with material suppliers to ensure the right resin is selected that provides the most value,
- We build tooling in house to ensure the right tooling is used for each application.
- We have secondary process resource, including painting, printing, coating, assembly and experience with high-volume runs, to minimize costs throughout the manufacturing process.
Injection molding service
MUYOUNG has variety of ton injection molding machines resource from 18T-2000T, which including special injection molding method:
A component of the injection molding system
The hot runner system is generally composed of hot nozzles, manifolds, temperature control boxes and accessories, etc. The hot nozzles generally include two types: open hot nozzles and needle valve hot nozzles, because the form of hot nozzles directly determines the choice of hot runner system and the manufacture of the mold, so often correspondingly the hot runner system is divided into open hot runner system and Needle valve hot runner system.
Many conditions are considered when selecting a hot runner, such as: different plastic properties, shape, size, thickness, weight of the product, cavity arrangement and gate location.
Advantages:
1、Saving raw material and reducing cost,
2、Shorten molding cycle and improve machine efficiency,
3、Improve the surface quality and mechanical properties of products,
4、It is not necessary to use the three-plate mold that can use the point gate,
5、Economically mold single products with side gates,
6、Improve the degree of automation,
7、The gate sealing can be controlled by needle valve type gate,
8、The quality of injection molded parts of multi-cavity molds is consistent,
9、Improve the surface aesthetics of injection molded products,
10、Can use smaller injection pressure, which can effectively reduce the post-deformation of thin-walled products,
However, every technology has its own disadvantages, and hot runner technology is no exception,
1, the mold structure is complex, high cost, high maintenance costs,
2、It takes a period of time for the process to stabilize before the machine is turned on, resulting in more scrap at the beginning,
3、In case of melt leakage and heating element failure, it will have a greater impact on product quality and production schedule,
The third disadvantage above can be reduced by purchasing top quality heating elements, hot runner plates and nozzles and by careful maintenance when using them,
2K mold: Two plastic materials are injected on the same injection molding machine, and molded twice, but the product only comes out of the mold once. Generally this molding process is also called double material injection, usually completed by 1 set of molds, and requires a special two-color injection molding machine.
2K mold compare with over molding: Two plastic materials are not necessarily injected on the same injection molding machine and molded in two times; the products are taken out from one set of molds and then put into another set of molds for the second injection molding. Therefore, generally this molding process is usually completed by 2 sets of molds, without the need for a special two-color injection molding machine.
Remark on design 2K mold:
1, Cavity’s two shapes are different, respectively molding 1 kind of products.
And Core’s two shapes are exactly the same,
2, the mold’s front and back die must match after rotating 180º with the center. This checking action must be done when designing,
3,pay attention to the position of the top stick hole, the minimum distance 210mm. large molds must increase the number of top stick holes appropriately. And, because the top stick that comes with the injection molding machine itself is not long enough, so we must design a longer top stick in our mold, the top stick is about 150mm long out of the bottom plate of the mold embryo,2 positioning rings must be designed on the bottom plate of the back mold,
4,the total thickness of the front mold panel plus A plate should not be less than 170mm, please check carefully the other reference data of this type of injection molding machine, such as the maximum mold thickness, minimum mold thickness, top stick hole distance, etc,
5, the water outlet of the three-plate mold should be designed to be able to release the mold automatically. Particular attention should be paid to the reliability of the demoulding action of the soft rubber water outlet,
6, the depth of the front side SPRUE should not exceed 65mm, and the distance from the top of the SPRUE to the center of the mold embryo should not be less than 150mm,
7,When designing the CAVITY for the second injection, in order to avoid the CAVITY from inserting (or rubbing) the glue position of the product that has been molded for the first time, you can design a part to avoid the hollow. However, the strength of each sealing position must be carefully considered, i.e.: in the injection molding, will there be a deformation of the plastic under the large injection pressure, resulting in the possibility of the second injection molding may have a batch front,
8, When injection molding, the size of the first injection molded product can be slightly larger so that it can be pressed tighter with another CAVITY in the second molding to achieve the role of sealing glue,
9, pay attention to the second injection, whether the flow of plastic will impulse the first time already molded products, so that its glue position deformation? If there is this possibility, must find ways to improve,
10, in the A, B board before the mold, pay attention to the front mold Slider or Lifter will be reset first and crush the product? In this case, we must find a way to make the A and B plates close the mold first, and then the Slider or Lifter of the front mold can be reset.
Two plastic materials are not necessarily injected on the same injection molding machine and molded in two times; the products are taken out from one set of molds and then put into another set of molds for the second injection molding. Therefore, generally this molding process is usually completed by 2 sets of molds, without the need for a special two-color or two kind material injection molding
Some products require inserts to be molded into them, typically metal, ceramic or plastic parts that can be inserted into molten thermoplastics to form multi-material, robust parts with additional functionality. For example, metal inserts with threads can be molded into parts that allow them to be attached to other parts.
Insert molding can reduce costs by embedding auxiliary parts into the plastic injection molding process, rather than installing the parts after molding. By integrating the insert at the time of molding, the part becomes stronger than if it were staked after molding. Of course, the insert must be able to withstand the heat and pressure of the injection molding process.
Insert molding is naturally a more complex process than standard injection molding, so some injection molding companies have more experience in this process than others. For small-volume production runs, machine operators can hand-load inserts into the mold prior to the plastic injection cycle. However, for high-volume production runs, automated machines are often used to place the insert into the mold.
Gas Assisted Injection Molding is a process that uses an inert gas to form one or more hollow channels within an injection molded plastic part. At the end of the filling phase, the gas is injected into the static liquid core of the molded part. From there, the gas flows along the path of least resistance and replaces a thick molten jet with a gas-filled channel.
In some cases the injection gate has to be placed in an area on the ejection side of the mold. The simplest option then is usually to make the mold with what we call reversed injection. In this mold type the ejection system is in the machine on the injection side with a hot runner placed through it. It is not possible to use the integrated ejection couplers of the machine so usually these molds have hydraulic cylinders added to move the ejection plates. There are cases that instead of cylinders there are chains added to a mold to perform the ejection while the mold is opened.
Injection molding Material
We have extensive experience in analyzing the properties of thermoplastic and thermoset materials, all of which are genuine materials produced in China by importers or material suppliers, including:
Thermoplastic:ABS、ABS/PC、PA、PA6、PA6GF、PP、PE、PVC、POM、PC、PS、PMMA、HDPE、AS、POE、PPO、PBT、TPU、ULTEM、PSU、PEEK……
Thermoset: Silicone 30,40,50,60 and 70 shore and other medical grand silicone.
How to choose building prototype mold or mass production mold?
Prototype mold
- Need to test product design, product material, assembly function, market feedback, etc.
- Need production volume of 10-50K;
- Need faster lead time and lower cost;
- Complex design accepted;
- Molds can be left in our company for injection molding or export;
Mass production mold
- Production quantities in 20K-1 million,
- The material of product is special,
- High precision products demand,
- Tooling cost is higher than prototype mold, but the product unit cost is lower;
- Complex design accepted,
- Molds can be left in our company for injection molding or export.
Our Clients testimonials
What They Are Saying
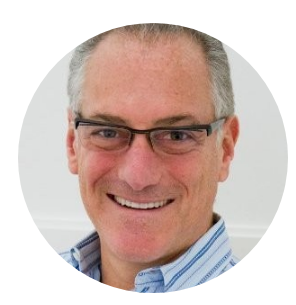
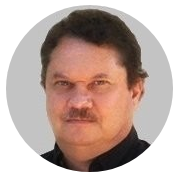
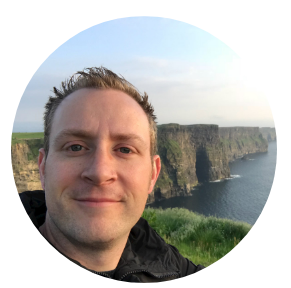
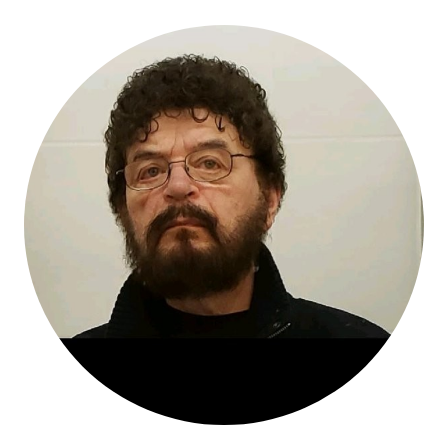
Let's raise your profits to next level Now→
Muyoung Mould will provide the following service when you send us your requiry.
Free DFM Feedback with Your Quote
Products Tolerance ±0.005mm
Full-automatic molding;
Low-Maintenance molds;
Modification price is reasonable;
Keep completive price;
Delivery Door to Door
Ask For A Quick Quote
We will contact you within 1 working day, please pay attention to the email with the suffix “sales@mu-mould.com”.
Upload Your 3D Files
We accept the 3D model with file formats: STEP(.stp), IGES(.igs), PRT(.prt),X_T(.xt),STL(.stl),
2D drawing format: PDF、DWG、DXF, The maximum supported file size is 80MB, for large or multiple files, please place into folder and compress into a ZIP or RAF files.