Insert molding
- Home
- Insert molding
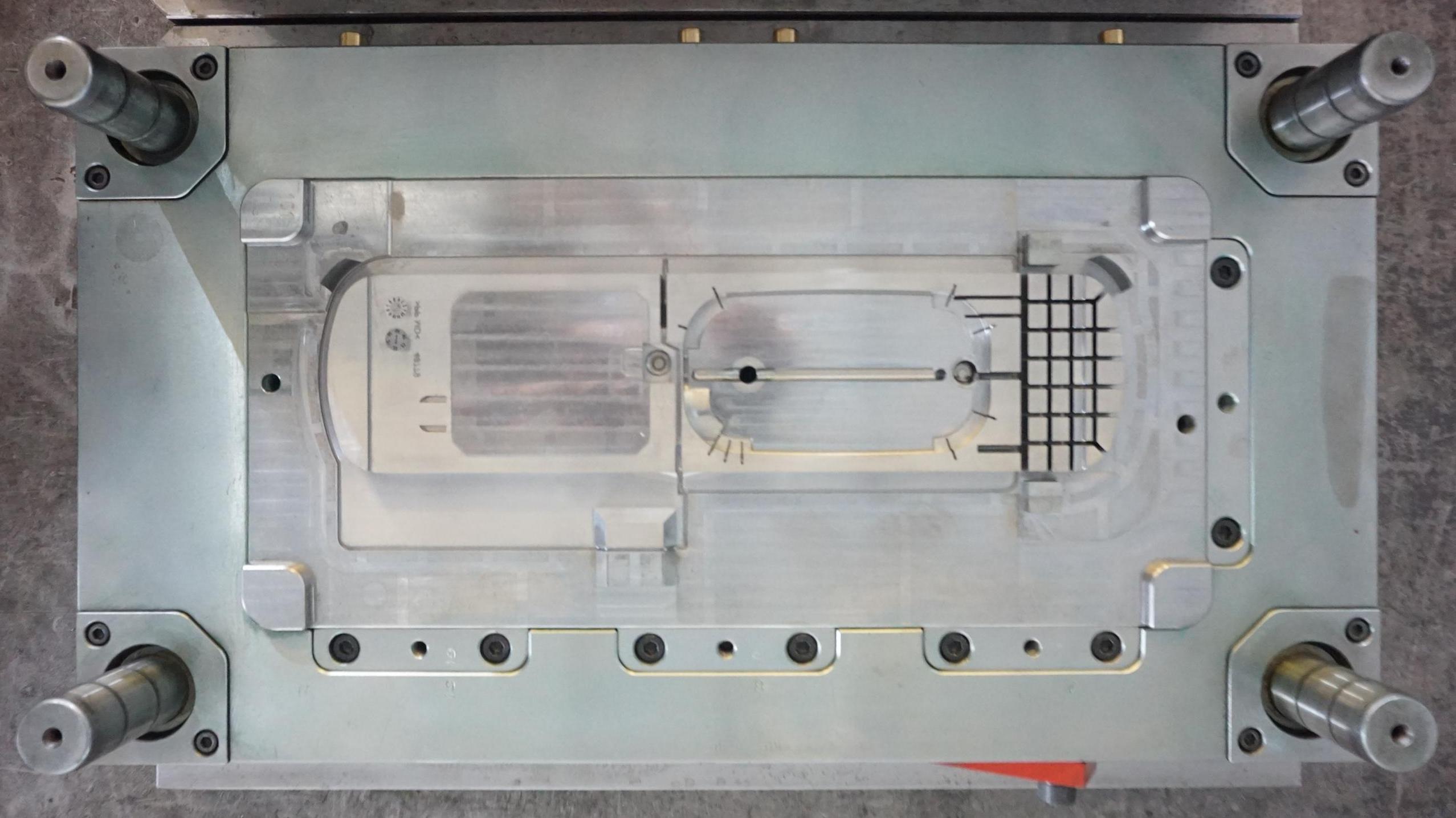
What is inserting over molding?
Insert molding is a molding process in which a pre-formed insert is placed in a mold before a second material is injected, and the molten material is joined with the insert and cured to make an integrated product. The material of insert molding is mainly metal or brass, but it is not limited to metal, but also wire, plastic, glass, wood, wire coils, electrical parts, etc ……
What are the advantages of insert molding?
- The combination of the ease of molding and bending of resin and the rigidity, strength and heat resistance of metal can make complex and delicate metal-plastic integrated products.
- In particular, the combination of the insulating properties of resin and the electrical conductivity of metal enables the molded products to meet the basic functions of electrical products.
- The prior molding combination of multiple inserts makes the post-engineering of product unit combination more rational.
- For rigid molded products and flexible molded products on rubber gaskets, injection molding on the substrate makes it possible to eliminate the complicated work of arranging the sealing area, making it easier to automate the post-process assembly.
- Since the molten material is joined to the metal insert, the gap between the metal insert can be designed to be narrower than that of the press-in molding method, and the reliability of the composite product molding is higher.
- Select the appropriate resin and molding conditions, even for products that are easily deformed and broken (such as glass, coils, electrical parts, etc.), the resin can be sealed and fixed.
- Select the appropriate mold structure, the inserted products can also be completely sealed into the resin.
- The combination of vertical injection molding machine, robot, insert molding device, etc. can mostly realize automatic production.
What do we need to pay attention to in the design of automatic insert molding system?
- Metal insert molding is prone to uneven shrinkage rate, so the limit test of shape and dimensional accuracy of important parts should be done beforehand.
- The metal insert is easily deformed and shifted during the injection process, so the mold composition and the design of the mold shape that can easily keep the metal insert should be fully considered. For products whose insert shape cannot be changed, prior testing is indispensable.
- In the case where the metal inserts are arranged separately and a conveyor is used, the contact between the metal inserts and between the inserts and the vibrating ball may cause slight damage to the surface of the inserts and affect the quality of the product. The quality tolerance range should be confirmed in advance.
- The jaggedness, warpage, material thickness difference, diameter difference, and thickness difference caused by gilding process of metal insert should be measured in advance. On this basis, the design of the automation device and the design of the mold structure should be selected.
- Predictable matters such as mold gate position, molding cycle and other constraints on mold structure should be solved or improved in advance as much as possible.
- It should be confirmed whether the metal insert needs to be preheated or dried. The purpose is to ensure the quality of the product and the stability of the molding.
- The various testing devices installed in the mold are used to ensure the stability of the molding action under the influence of heat, force, vibration and other environmental conditions, and it should be confirmed whether they are used.
Muyoung mould is tooling mold maker and also a plastic product suppliers, we are ready for work with about insert molding project.
Did you like this Work? Please Share